انواع شمش فولادی و فرآیند تولید آن در کارخانه
شمش مقطعی است که به عنوان پیشساز انواع مختلف مصالح فولادی کاربرد دارد. در حقیقت این محصول مهمترین مقطع و مادهی موجود در زنجیرهی تولید فولاد است که به روشهای مختلفی تولید میشود؛ بنابراین آشنایی با شمش فولادی و روشهای تولید آن از اهمیت زیادی برای فعالان حوزه آهن آلات و فولاد برخوردار است.
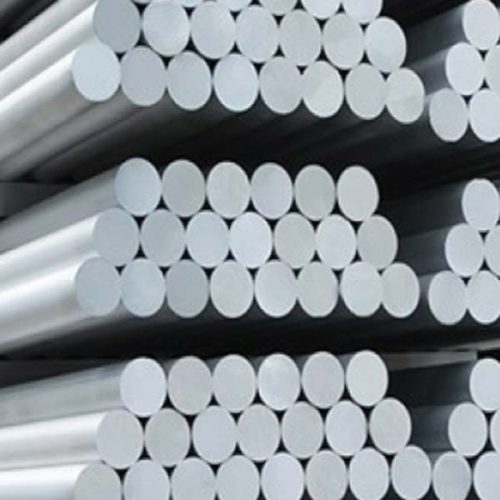
نحوهی تولید شمش فولادی
ذوب در کوره اصلیترین و در عین حال مقرونبهصرفهترین روش تولید شمش فولادی است که در کورهی بلند، کورهی قوس الکتریکی و کورهی ذوب القایی قابل انجام است. این سه کوره تفاوتهایی با یکدیگر دارند که در این قسمت به بررسی آنها میپردازیم.
تولید شمش فولادی با استفاده از کوره بلند
بعد از اکسيژن بازی نوبت به گرمادهی و اکسیداسیون میرسد. با انجام این مرحله، ناخالصیها حذف میشوند. برای جذب ناخالصیهای موجود، مقداری آهک به ترکیب اضافه میکنند که با ناخالصی ترکیب شده و سرباره تولید میکند. در مرحلهی آخر فولاد تولید شده از حفره کنورتور خارج میشود.
مزایا و معایب استفاده از کوره بلند
+ جداسازی مناسب ناخالصیها
+ امکان تولید شمش فولادی در حجم بالا
– درصد بالای ضایعات
– انعطافپذیری نهچندان مناسب فولاد تولید شده
– تولید گازهای آلاینده قوی
تولید شمش فولادی با استفاده از کوره ذوب القایی
در این روش از یک میدان مغناطیسی برای ذوب قراضهها استفاده میکنند. به دور این کوره یک سیم پیچ القایی بسته شده که با کمک جریان الکتریسیته با فرکانس بالا، میدانی مغناطیسی به همراه گرما تولید میکند. در نهایت این دمای بالا به درون کوره منتقل شده و منجر به ذوب فلزات میشود.
مزایا و معایب استفاده از کوره بلند
+ عملکرد آسان
+ نبود آلودگی صوتی
+ راندمان حرارتی بسیار بالا
– فرکانس بالای جریان الکتریکی و قیمت بسیار بالای کوره
– عدم امکان تولید سرباره
تولید شمش فولادی با استفاده از کوره قوس الکتریکی
در این روش اندکی ضایعات فولادی که شامل قراضههای خانگی، صنعتی و کهنه هستند و آهن اسفنجی،آهن قراضه با استفاده از جرثقیل به داخل کوره منتقل میشوند. کوره قوس الکتریکی به شکل حمام بزرگ و کم عمقی است که در قسمت بالایی آن الکترودهای کربنی وجود دارد. بعد از اضافه کردن ضایعات به کوره، الکترودها به سمت پایین حرکت کرده و به این ترتیب منجر به برقراری جریان الکتریکی و در نهایت ذوب فلزات در دمای ۴۱۰۰ درجه سانتیگراد میشوند.
با توجه به این که در این روش امکان تولید انواع شمش آلیاژی وجود دارد و شمش به دست آمده از این روش نیز با کیفیت تر از شمش روش های تولیدی دیگر است؛ فولاد بافق برای تولید و خود از انواع شمش تولید شده با روش قوس الکتریکی استفاده می نماید. این شمش ها هر چند در بازار قیمت بالاتری نسبت به سایر شمش ها دارند اما کلاف و میلگرد بدست آمده از آن ها بهترین خواص مکانیکی را ارائه می دهد.
مزایا و معایب استفاده از کوره بلند
+ انعطافپذیری بالای کوره
+ امکان تولید انواع شمش فولادی
+ کنترل دمای فولاد مذاب
+ کیفیت بالاتر فولاد تولید شده در مقایسه با روش کوره بلند
– هزینهی بالا
برندهای تولیدکننده شمش فولادی در ایران
مجموعههای مختلفی در ایران در زمینهی تولید شمش فولادی فعالیت میکنند که از جملهی آنها میتوان به موارد زیر اشاره کرد:
- ذوب آهن اصفهان
- فولاد خراسان (نیشابور)
- فولاد سیرجان
- فولاد مبارکه اصفهان
- فولاد خوزستان
- گروه ملی صنعتی فولاد ایران
- فولاد هرمزگان
- مجتمع فولاد شاهین بناب
- (در حال ساخت)
شمش فولادی درحقیقت اولین محصول فولادی قابل حمل به شکل جامد است که روشهای مختلفی برای تولید آن وجود دارد. آشنایی با این روشها برای تمام سرمایهگذاران و فعالان بازار آهنآلات ضروری است. با توجه به کیفیت بالای شمش تولیدی با روش قوس الکتریکی، فولاد بافق در حال ساخت کارخانه ذوب و ریخته گری فولاد به روش قوس با ظرفیت 1 میلیون تن در سال است. با تکمیل این پروژه ضمن تامین نیاز کارخانه نورد میلگرد و کلاف فولاد بافق، سایر کارخانجات نیز می توانند از شمش قوس تولید شده یکی از کاربرد شمش فولادی ساخته شده در جهان است. مطالعه تاریخ نشان میدهد ساخت شمش برای اولینبار در زمان هخامنشیان انجام شده است؛ اما ساخت شمش تنها مربوط به هخامنشیان نبوده است و اکتشافات باستانی نشان میدهد استفاده شمش طلا و نقره به عنوان پول در جهان رواج داشته است.
همه ما احتمالا در فیلمها و یا تصاویر ضبط شده از بانکهای بزرگ جهانی هرمهای چیده شده از شمش طلا را دیدهایم؛ شمشهای زرد طلا که به شکل منشور چهارپهلو که مانند آجر رویهم قرار گرفتهاند، چنین ایماژی تصویریترین تعریف از شمش است که میتوان بیان کرد؛ اما یکی از صحیحترین تعریفها توسط فرهنگ مریام وبستر بیان میشود:
«حجمی از فلز که در فرآیند ریختهگری به شکل یک قالب مشخص تولید میشود تا حمل و نقل، ذخیره کردن و استفاده از فلز آسانتر اتفاق بیفتد.»
کاربردهای انواع شمش فولادی
همانطور که دانستید شمش فولادی انواع مختلفی دارد بسته به نوع شمش کاربردهای آنها نیز متفاوت خواهد بود. دیاگرام زیر کاربردهای مختلف بیلت، بلوم و اسلب را نشان میدهد.
انواع روش تولید شمش فولادی:
شمشهای فولادی در دو کوره القایی و قوس الکتریکی تولید میشود:
تولید شمش فولادی با استفاده از کوره بلند
- ناخالصیها بهخوبی جدا میشود.
- امکان تولید با حجم بالا وجود دارد.
معایب کوره بلند:
- درصد ضایعات در این روش بسیار بالا است.
- فولاد تولید شده از انعطاف خوبی برخوردار نیست.
- گازهای تولیدی در این روش آلایندههای قوی محسوب میشوند.
- قراضههای خانگی
- قراضههای صنعتی
- قراضههای کهنه
کوره قوس الکتریکی به شکل یک حمام بزرگ کمعمق است که الکترودهای کربنی بالای آن قرار گرفتهاند؛ زمانی که قراضه و آهک وارد کوره شد، الکترود به پایین آورده میشود. همزمان با پایین آمدن الکترودها جریان الکتریکی برقرار میشود و این جریان الکتریکی موجب ذوب فلزات میشود. توجه داشته باشید که دمای الکترود حدود ۴۱۰۰ درجه سانتیگراد است و همین دمای بالا سبب ذوب فلزات میشود.
مزایای کوره قوس الکتریکی:
- فرآیند انعطافپذیری است که میتوان انواع شمش فولادی را تولید کرد.
- دمای فولاد مذاب تحت کنترل است
- کیفیت و ضایعات فولاد در کوره قوس الکتریکی از کوره بلند بهتر است.
معایب کوره قوس الکتریکی:
- کیفیت فولاد به مواد قراضه ربط دارد.
- هزینه انرژی به دلیل استفاده از برق و مدتزمان بیشتر ذوب فولاد بسیار بالا است.
- ناخالصی بیشتر وارد فولاد شده و کیفیت فولاد کم میشود.
تولید شمش فولادی با استفاده از کوره ذوب القایی (IMF)
میدان مغناطیسی در این روش موجب ذوب قراضهها میشود، یک سیمپیچ القایی که به دور کوره پیچیده شده است در هنگام وجود جریان الکتریسیته با فرکانس بالا میدان مغناطیسی ایجاد کرده و گرما تولید میکند. دمای بالا به داخل کوره منتقل شده و ذوب فلزات را موجب میشود.
مزایای کوره القایی:
- عملکرد این کوره بسیار راحت است.
- عملیات ذوب بدون ایجاد آلودگی صوتی انجام میشود؛ برعکس کوره قوس الکتریکی که دارای صدای زیادی است.
- راندمان حرارتی در این کوره بسیار بالا است.
معایب کوره القایی:
- به دلیل اینکه برای عملکرد کوره نیاز به فرکانس بالای جریان الکتریکی است، لذا قیمت کوره بسیار بالا است.
- از آنجا که سطح فوقانی مذاب دارای تلاطم و دمای آن سرد است، امکان تولید سرباره نیست.
مراحل تولید فرآوردههای میانی (بیلت، بلوم و اسلب)
بعد از آن که شمش فولادی در هرکدام از روشهای فوق تشکیل شد، حال نوبت آن است که شمش تبدیل به یک فرآورده میانی شود که همان اسلب بیلت و بلوم است.
ریختهگری مداوم: به این نوع از ریختهگری ccm گفته میشود، در این روش بعد از ذوب فولاد تمام مراحل به طور پیوسته صورت میگیرد. بعد از تولید فولاد مذاب، مواد وارد محفظهای به نام تاندیش میشود. تاندیش جریان مداوم مواد به مرحله ریختهگری را به عهده دارد. بعد از آنکه مواد از تاندیش تغذیه شدند وارد قالبهای مسی میشوند. قالب مسی شکلدهی مواد مذاب و سرد کردن مواد را به عهده دارد.
در زیر قالب ناحیه خنککننده وجود دارد، در این ناحیه آب سرد بهوسیله نازل به روی مواد مذاب پاشش میشود. پاشش آب بهصورت پودری بوده و با فشار ۰/۲ تا ۰/۳ مگاپاسکال انجام میشود. پیشروی آب در مواد مذاب قالب گرفته تا هسته شمش صورت میگیرد برای همین در زمان خروج مواد مذاب از بخش خنککننده، مواد شکل سیال خود را از دستداده و به حالت جامد در خواهد آمد. با جامد شدن مواد حال نوبت آن است که در یک مسیر خطی شمش دو سطح بالایی و پایینی شمش مسطح شود برای این کار شمش از غلتکهای مخصوص عبور کرده و بعد از صاف شدن بهاندازهای که نیاز است (ابعاد بیلت، بلوم و اسلب) برش داده میشود.
اکستروژن: از جمله روشهای شکلدهی فلزات اکستروژن است. در این روش به سه صورت گرم، داغ و سرد عملیات انجام میشود. معمولا از اکستروژن سرد برای تولید شمشال استفاده میشود. در این روش یک چاله زمینی حفر میشود و شمش وارد محفظه پرس شده و بهصورت عمودی به شمش فشار آورده میشود. خروجی به سطح مقطعی خواهد بود که نیاز است. استفاده از اکستروژن کمتر معمول است.
تولید بیلت بلوم اسلب در ایران و جهان
اگرچه اقتصاد جهان متلاطم و دچار رکود شده است؛ اما المانها نشانگر رشد درخواست جهانی فرآوردههای میانی تولید فولاد است، طبق گزارش روزنامه دنیای اقتصاد نرخ درخواست اسلب در جهان در حال افزایش است، ضمن آنکه بیلت نیز مانند اسلب با رشد درخواست مواجه بوده است. فراموش نباید کرد که این فرآوردهها در تولید میلگرد، تیرآهن و ورقهای فلزی نقش اساسی دارند و با رشد اقتصاد و فعالشدن بازارهای جهانی بعد از موج کرونا، تولید در بخش ساختمان و صنایع اتومبیلسازی بالاتر خواهد رفت، برای همین نیاز به فلزات ذکر شده بالاتر خواهد رفت. در کشور ایران نیز سال گذشته نرخ تولید بیلت و بلوم، رشد داشته است؛ بهطوری که اکثر کارخانههای تولیدی نرخ رشد بیلت بالاتر از سالهای قبل بوده و تولید اسلب در ایران از مرز ۷ میلیون تن گذشته است.
اگرچه برای ایران آینده بازار کمی سخت است، زیرا هنوز مسائلی مانند برجام و انتخابات ریاستجمهوری در سال آینده مشخص نیست و پیشبینی بازار برای سال آینده سخت است؛ اما شواهد نشان میدهد رکود تورمی در ساختمان در سال آینده بر درخواست میلگرد و تأثیرگذار باشد و درخواست برای بیلت و بلوم را کاهش دهد؛ بنابراین انتظار میرود همچنان تولید اسلب در آینده نیز بالا باشد.نیاز سالانه جهانی به فولاد و تولیدات همگروه فولاد در حال افزایش است، در کشور ما نیز توجه به این تولیدات افزایش پیدا کرده است.
تبدیل شمش فولادی به محصولات نهایی، امروزه در بسیاری از کارخانهها رواج پیدا کرده است؛ اما تولید هر محصول نهایی با کیفیت نیازمند فرآوردههای میانی تولید فولاد است، از آنجا که شرکتهای مختلفی شمش فولادی تولید میکنند محصولات با استانداردهای مختلفی در بازار وجود دارد، برای ما بنویسید کدام شرکت فولادی تولید بلوم، بیلت و تولید اسلب بهتر و با استاندارد بهتری دارد. به علاوه با راه اندازی کامل کارخانه ذوب، امکان ورود مستقیم شمش داغ از بخش ذوب به نورد فراهم می گردد که ضمن کاهش انبارش و اتلاف زمان، صرفه جویی قابل توجهی در مصرف گاز طبیعی کارخانه صورت می پذیرد.